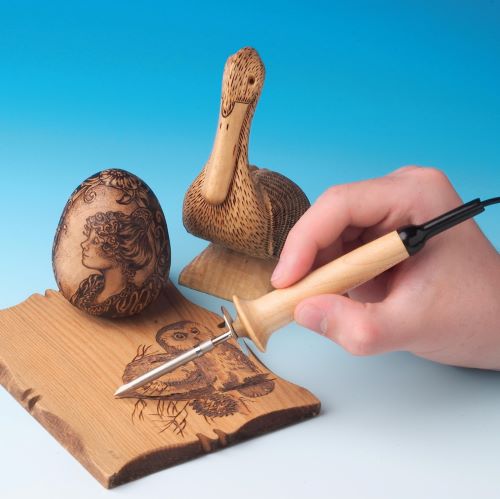
If you are interested to create unique, beautiful pieces for you home, you might want to learn more about pyrography using cedar. This ancient art involves the burning of intricate designs and ornaments into wood. It dates back to 17th century. The resultant burn marks make beautiful dark designs. This can include landscapes as well as portraits. This technique has been around for centuries, and is a popular choice for home decor.
Yoko sugi ban
In 18th century Japan, a technique known as shou sugi ban is used to preserve wood by charring the surface. This results in a wood surface that is richly charcoal black. It can also give it a cracked appearance or alligator skin. Japanese cedar is used most often for its rustic look. However other wood species could be used with greater success. The wood's resistance to future damage is strengthened by the controlled charring process, which makes it an ideal preservation technique.
Shau sugi ban
The method of removing char is the most noticeable difference between traditional sanding and shou-sugi ban. Shau-sugiban woodworkers remove the charred layers with wire brushes. Others use coarse sandpaper. Either way you will need to remove enough char so that the brownish black color of the bottom layer can be revealed. The result will look like an alligator's skin, so sanding is essential to remove any excess char.
Shau sugi ban on cedar
The wood finish of shou sugi bans pyrography is attractive, but it also has practical implications. The charred wood can be traced throughout a building and can be inhaled by anyone who is present within the space. To combat this problem, pyrographers are beginning to use propane torch in addition to the traditional wood-burning method. Here is a look at the differences between the two styles.
Yaki sugi bans basswood
The centuries-old Japanese technique of yakisugi ban (on cedar) can give wood beauty and strength. Though sometimes referred to as Shou sugi ban, this process involves charring the surface of wood to create a beautiful pattern. The practice is so widespread in Japan that cedar has been used in many shousugi ban projects. Satoshi Kmura, operations director at a Japanese timber company, describes why shou shugi ban is so common and what it means to woodworkers.
Yakisugi bans blue stain pine

This process is also known as shou suugi ban and uses fire to preserve wood. Traditionally, cedar is used to perform shousugi ban. But other woods can also be used. Even though cedar is the most traditional wood for this purpose, yakisugi can also be used with maple, ash or birch. This technique is popular among traditional Japanese craftspeople.
Shau sugi ban on basswood
Charring a piece of cedar gives it a rich, deep black color with a distinctive crackled surface. Cedar naturally sheds water and repels pests, but the charred surface also has sculpting properties. There are two options for charred wood: untreated or reclaimed. A cedar panel can also be treated to achieve a subtler burnt wood finish.
Shau sugi ban on jelutong
Shou sugi bans wood-pyrography. The technique improves wood's natural patterns. Additionally, charred wood is more durable because of the thicker carbon layer. This is dependent on the timber species and environment in which the treatment is performed. Shou sugi Ban is an environmentally friendly way of treating wood.
FAQ
Is it difficult to start my woodworking business?
It's not easy to start your own woodworking business. There are many regulations and legal requirements that you will need to comply with. But, this doesn't mean you need to go through all of the trouble of setting up your business. Many people decide to join established businesses. You will only have to pay membership fees, taxes, and other charges.
What tools should I start with when becoming a woodworker?
Woodworking requires patience and practice. Learning how to use the various tools and techniques necessary for woodworking takes patience.
There are many different types of woodworking equipment available on the market today. Some prefer to use power tools, while others prefer to use hand tools.
The choice is yours, but you must ensure you choose the right tool for the job. Start with a basic set if you don’t have any previous experience.
A router is a tool that cuts intricate shapes in wood. You can also learn how to use it. These routers can be purchased at most hardware and home improvement stores.
What kind of tools are used to carpenters?
Carpenters most often use a tool called a hammer. A hammer helps to carpenter pound nails into the wood. It also helps them hold pieces together while they are working on a project. Other tools include clamps and pliers, screwdrivers as well as measuring tape, pencils and saws.
Is it possible to learn woodworking by yourself?
You can learn everything best by doing. Woodworking is an art that takes patience, practice, skill and experience. It takes time to master any craft.
The best way to learn how to do something is actually to do it. Start small and then build upon what you've learned.
How can my shop be organized?
First, make sure you have a designated space for tools storage. Make sure your tools are clean and free of debris and dust so they can be used properly. Use pegboard hooks to hang tools and accessories.
Statistics
- Overall employment of woodworkers is projected to grow 8 percent from 2020 to 2030, about as fast as the average for all occupations. (bls.gov)
- In 2014, there were just over 237,000 jobs for all woodworkers, with other wood product manufacturing employing 23 percent; wood kitchen cabinets and countertop manufacturing employing 21 percent. (theartcareerproject.com)
- If your lumber isn't as dry as you would like when you purchase it (over 22% in Glen Huey's opinion…probably over 10-15% in my opinion), then it's a good idea to let it acclimate to your workshop for a couple of weeks. (woodandshop.com)
- The best-paid 10 percent make $76,000, while the lowest-paid 10 percent make $34,000. (zippia.com)
External Links
How To
How to make wood joints
This tutorial will show you how to join two pieces of wood together. We will be using the "pocket-hole joint", which involves drilling holes in wood and then gluing them together. If your wood has a straight grain, smooth surface, you can use this method. You may want to consider other methods, such as dowel joining. These are the steps
-
Drill Pocket Hole Joints. You will need to measure and mark the exact location of your pocket hole joint. Use a jigsaw or handheld drilling machine to drill 3/8 inch deep holes at the ends of each wood piece.
-
Sand Smooth. The wood's edges can be sanded to prevent splitting.
-
Glue Together Apply glue on both sides of the wooden plank. Allow it to sit for approximately 5 minutes before you clamp the pieces together.
-
Attach the Pieces together. After the glue has dried thoroughly, secure the pieces so that they are flush.
-
Trim Joinery. Trimming the joinery after glue has completely dried.
Be sure to leave enough space between each piece so that they can be turned inside-out.