
It can be difficult cutting rough lumber and loading it into your car is not easy. Bring your tape measure, hand saw and saw to the hardware store. Also, make sure to buy extra boards in the event that the one you have purchased doesn't fit. Make sure you have the right knots and checks on your board. Otherwise, they might not fit as well as you would like. You don't want a board that is too small and has to be cut up again. This is a wasteful way to spend your time and money.
We save money!
A sawmill turns roughly 59% of the rough lumber into boards. The remainder of the log, which includes sawdust or bark, is considered waste. Even though a poor cut may result in more wasted wood, the amount should not exceed 20%. Here's how to estimate the amount wasted wood in a board. For a nominal 4-foot board, the sawmill should remove about 18% of its volume to achieve the desired lumber thickness and width.
One thing is that rough lumber does not come in the same dimensions. The dimensions of hardwood that you purchase from a big box retailer are often known. This allows for you to plan your project using the standard size. The rough edges of lumber can be uneven, which leads to wasted material. Also, rough-cut lumber is usually of a similar width. This results in a lot more lumber being wasted. And this waste can't be used later.
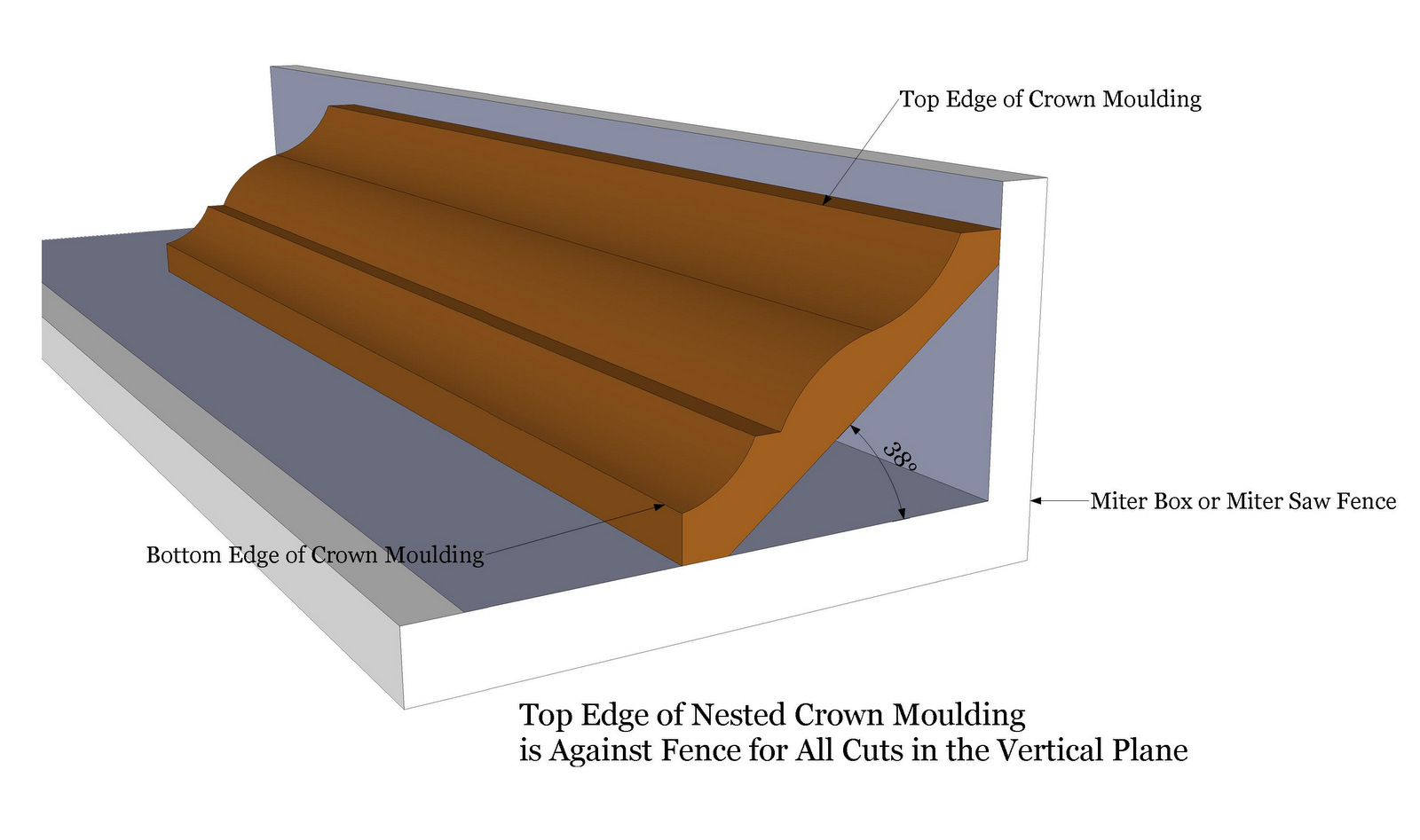
Preparation
The first step in preparing for cutting rough lumber is to measure the length of the material. Rough lumber might not arrive flat at the lumber yard. It may not have parallel sides or edges. This may mean that it will take several passes to flatten. One rule of thumb is to cut 1/16" per pass. If the lumber has concave edges, you can run it through a saw with the concave side down.
Generally speaking, rough cut lumber should be flattened to about 1/4" thick before the saw cuts it. After flattening the face, plane to the thickness of the finished board. Once you have measured the rough lumber's thickness, measure the finished width & length. Be aware of any imperfections and plan accordingly. Make sure to leave at least one-quarter inch of space between each board. Plan your project around the available boards. Hard to work with lumber that is too warped, bowed or twisted.
Cost
There are two types of lumber: dimensional lumber and rough-sawn lumber. Home improvement shops usually sell finished lumber but only rarely rough-sawn. Both types of lumber are often available at local sawmills and lumber yards. The main difference between the two types of lumber is the amount of work that they require to be processed. The cost of rough-sawn lumber is lower because it needs less processing. It's also much wider and more thin than finished lumber.
While purchasing lumber from a mill/lumber yard is usually cheaper, it is less likely that the lumber will be available in standard lengths. Making your own lumber can save you money over buying rough-sawn lumber. However it will require some space and additional power. Milling equipment can be noisy and requires training. You might want to check the zoning laws for your area before you start using your mill.
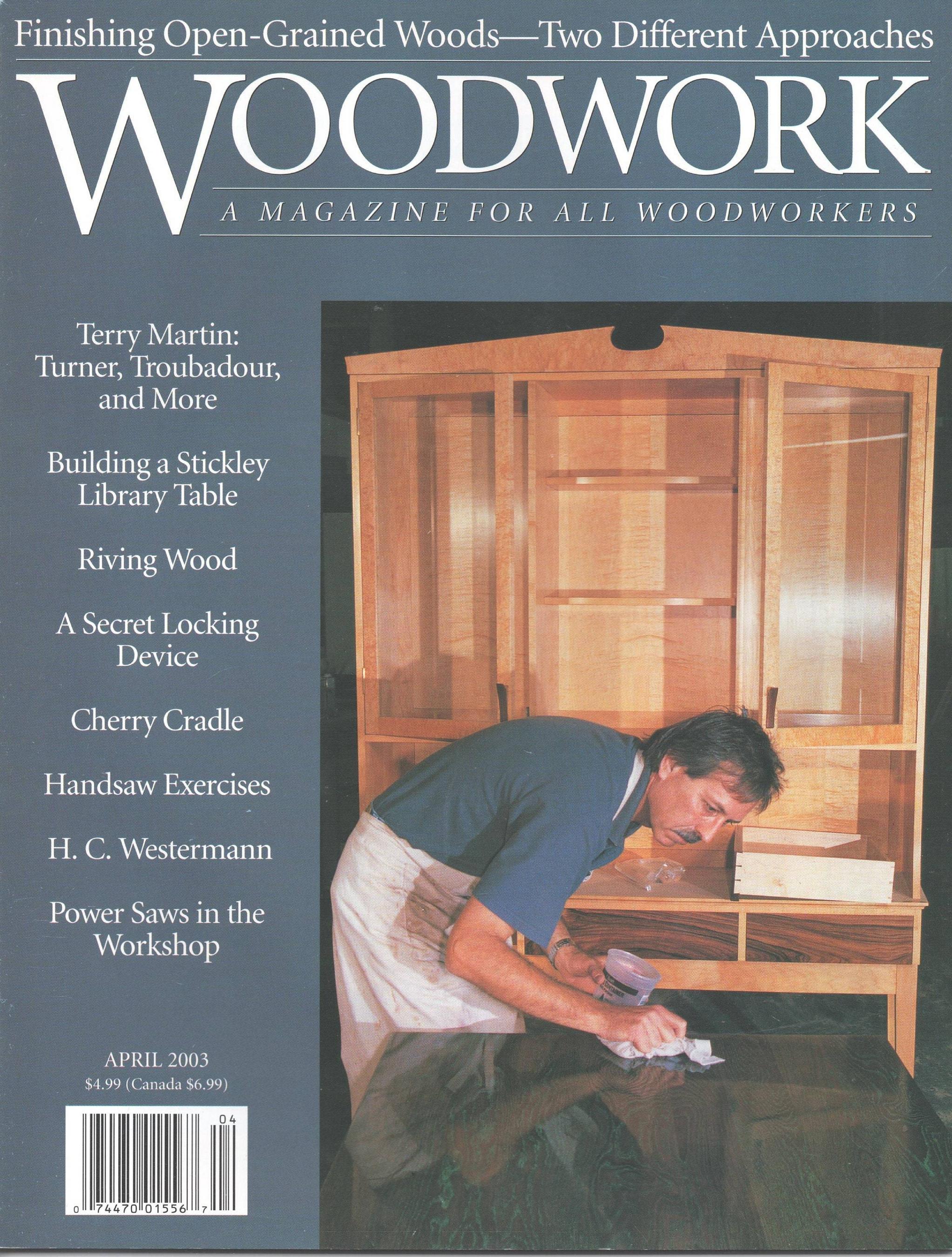
Source
There are many options for lumber purchases. There are many sizes and shapes to choose from, as well as different finishes. Rough sawn lumber for example is unfinished lumber that has not been sanded or finished and which has been cut into planks. This type of lumber tends to be stronger than other types because it carries extra moisture, but it is also thicker than surfaced wood. The following are some benefits of using rough sawn lumber for your woodworking projects.
The first is the availability and low cost. Rough lumber is not treated and is not usually sold at a hardware store. This type of lumber does have its advantages and disadvantages. This lumber is cheaper per board foot but less expensive by volume. Plus, it takes more time to finish than treated wood. You might also consider this option when deciding how much lumber you should purchase. Consider purchasing large quantities of rough sawn lumber and small amounts for finishing if you intend to use it for your project.
FAQ
What tools should you start with to become a woodworker
Woodworking is an art. It requires patience. It takes time and practice to master the various techniques and tools required for woodworking.
There are many different types of woodworking equipment available on the market today. Some prefer to use power tools and others prefer hand tools.
While you have the option to pick what you like, it is essential that you get the right tool for the job. You might start with a simple set of tools if you don't have much experience.
You might also consider learning how to use the router to create intricate shapes from wood. These can be found at most hardware shops.
Is it possible to open my own woodworking shop?
It's not easy to start your own woodworking business. There are many regulations and legal requirements that you will need to comply with. But, this doesn't mean you need to go through all of the trouble of setting up your business. Many people opt to join existing businesses instead. This allows you to join existing businesses and pay only membership fees.
What kind of wood should you use?
There are many wood types that are used in woodworking, including oak, maple and birch. Each wood type has its own characteristics which affect the final product's appearance and feel. Oak is a darker wood and tends to be more durable than other types. Birch is light and soft, while mahogany can be heavier and more dense. You can also choose between solid wood and veneers. Veneers are thin wood sheets that are glued together to form one layer.
Statistics
- Woodworkers on the lower end of that spectrum, the bottom 10% to be exact, make roughly $24,000 a year, while the top 10% makes $108,000. (zippia.com)
- In 2014, there were just over 237,000 jobs for all woodworkers, with other wood product manufacturing employing 23 percent; wood kitchen cabinets and countertop manufacturing employing 21 percent. (theartcareerproject.com)
- If your lumber isn't as dry as you would like when you purchase it (over 22% in Glen Huey's opinion…probably over 10-15% in my opinion), then it's a good idea to let it acclimate to your workshop for a couple of weeks. (woodandshop.com)
- Average lumber prices rose about 600 percent between April 2020 and May 2021. (familyhandyman.com)
External Links
How To
How to join two pieces of wood together without nails
Woodworking is a popular hobby. It's fun and relaxing because you can use your hands to make something useful from wood. Sometimes you may want to join two pieces together of wood without using nails. This article will help you to maintain the beauty of your woodwork projects.
First, remove any sharp edges from the wood pieces before you join them. Avoid leaving sharp edges that could lead to problems later. After you have completed this step, you are ready to glue your boards together.
When working with hardwood, glue should be applied only to one side. If you are using softwoods such pine or cedar, glue should only be applied to one side. Once you have applied the glue, press down on the boards until they are fully attached. Be sure to let the glue dry before you move on to the next step.
Once you've glued your boards together you will need to drill holes in the joints to accommodate screws. These holes will differ depending on the type and size of screw you are using. For example, if you intend to use 1/2-inch wood screws, you need to drill a hole that is at most 3/4 inches deep.
Once you've drilled your holes, you'll want to drive the screws through the joint and into the backside of the board. Avoid hitting the board's top surface. Otherwise, you could ruin the finish. Avoid hitting the screws' ends too often when driving screws. This will prevent the wood from splitting.
Now that your project is finished, you'll want to protect it from the elements. You have two options: seal the whole furniture piece or just the top. You'll want a product that lasts for many years. Oil-based varnishes are, among others, polyurethanes shellac, laquer, and other oil-based products.
These products can generally be found in any home improvement shop. Make sure you get the right product for your job. Remember that some finishes can be toxic, so you should not use them indoors. When handling certain finishes, wear protective gear.