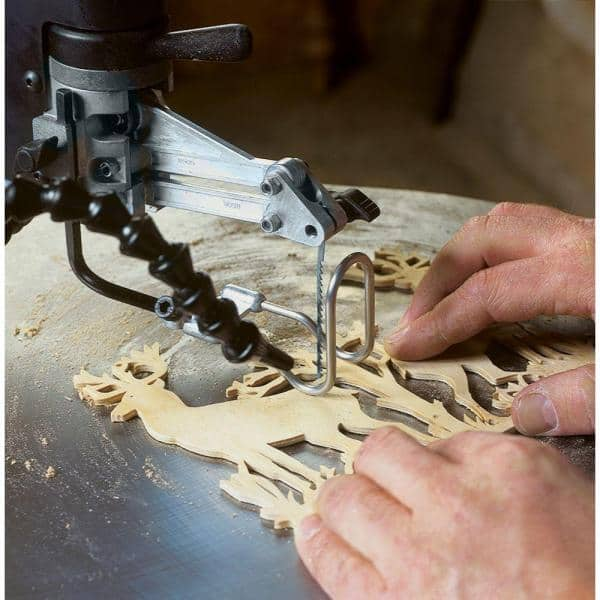
Scroll saw train patterns can be made in many ways. You need to consider the type of wood you want, how many sheets you need, and what size the pattern will be. To make the project even easier, scroll saw train patterns are available in full-size books. The patterns can be printed one side of a page to make it easy to cut from the book. These books are perfect for beginners as well as experienced scroll saw users.
Wood requirements
A wide range of woods is required to create scroll saw-train patterns. Cherry, walnut and oak are the most common woods. Birch is another good choice, however it absorbs stain in irregular patterns. For other projects, you may need to use exotic woods like mahogany or walnut. Not recommended is the use of fir plywood and luan. Cherry and walnut are good choices, as they are both affordable and have high strength to weight ratios.
Beginners should avoid cutting intricate patterns until they are more experienced. Beginning woodworkers should adhere to the lines drawn on the wood, and then slowly merge into them. It is important that you remember that scroll saw blades don't have the ability to cut straight lines. You must guide the wood onto the cutting table with your hand and not push it into the blade. You should be able to see the wood that your scroll saw can cut.
Pattern size
There are many Scroll Saw Train Patterns available on different websites. You can make a large yard art image or small scroll saw shelf projects depending on the project. There are many sizes of scroll saw train patterns to suit any project. Splitting the patterns on multiple A4 sheets or letter-sized sheets is possible for ease of use. These designs are also printable so you can print and cut them straight from the book.
A simple project is the best way to get started with scroll saws for beginners. There are many popular scroll saw patterns, including a coaster and hanger sets, a VW Beetle plaque, a VW Beetle plaque, a heart jewelry tree, and even a VW Beetle placket. These patterns can be printed for free. Build your masterpiece once you've found the right design. There are many options! Scroll saw patterns can be made in many sizes and shapes.
Required number of sheets

You can print out scroll saw pattern patterns to practice with large pieces. The designs are fully-sized and there are no inside cuts. These patterns eliminate the need to enlarge or save on paper. Print one side of the pattern and cut out any pieces you require. Next, use the copied copy to create practice pieces for larger projects. Remember that practice pieces do not have to be matched together.
Clear packaging tape is another option. It will help prevent wood fibers from getting stuck to the pattern. Some scroll sawers use painters tape. This is a weaker version of regular paper. Some others use a mixture of clear packaging tape and painters tape. In any case make sure you carefully read and understand the instructions. This way, you won't ruin your patterns.
Evolution of a scroll saw
The origins of the scroll saw are obscure, despite the fact that the first patent for a reciprocating steel blade was issued in Great Britain in 1829. While it's not known when the scrollsaw was first introduced in Western Europe, its earliest forms date back to prehistoric times when woodworkers used knives and saws to make complex cuts. This method of cutting wood is known as fretwork and dates back to the earliest civilizations.
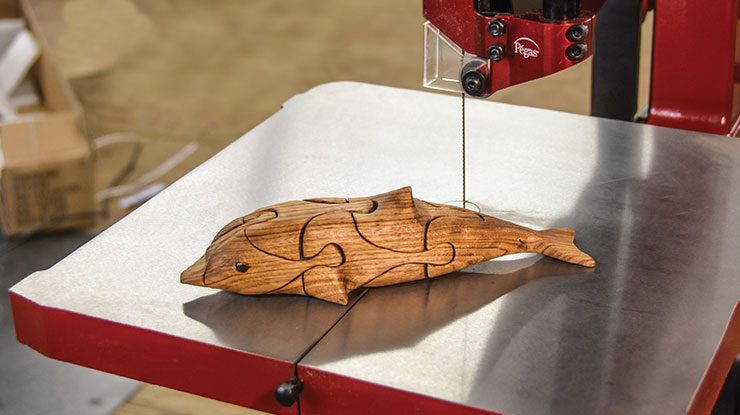
Scroll saws of today are capable to make complex cuts thanks their innovative design features. A lot of scroll saws come with tilting tables. This allows users to angle the material and create beveled edges. Some tilt up to 45 degrees and some tilt to the left, and some even tilt both ways. If the tilt is too much, you can flip the material to the other side and cut the bevel. Some models have an integrated sawstand so that users can work comfortably standing.
FAQ
Are there any other things I should know regarding woodworking?
It is easy to underestimate how much work it takes to make furniture. The hardest part of the process is actually finding the right wood. There are so many wood options that it can be difficult to choose the right one.
Another problem is the fact that not all wood has the same properties. Woods can warp, split, or crack over time. These things should be considered before you buy wood.
Which woods are good to use for furniture-making?
Woods are classified according their hardness. Softwoods include cedar, pine, cedar, and Cypress. Because they resist rot, softwoods can be used to make outdoor furniture. The hardwoods are oak, maple and mahogany. They are generally indoors as they don't weather well outside.
How does a beginner woodworker earn money?
Many people are looking to create their own furniture and start an internet business. However, if you're just getting into furniture building, there are other options than selling on Etsy. Sell at craft fairs or other local events. Or you could offer workshops for others who want to learn how to build their own furniture. You might be able to offer services like remodeling homes or making custom pieces for clients if you are a skilled carpenter.
How do I get started with woodworking?
You can learn the most effective way to build furniture by actually building it. While you will need tools and make mistakes, you will eventually master the art of building furniture.
You should first choose the project you wish to complete. You could make something as simple or complex as a box. Or you could build a whole entertainment center. Once you have chosen a project, locate a local woodworker who is skilled in this kind of work. Ask your local woodworker to help you determine the right tools for you and where they are located. You might even ask whether there's someone else you can talk to who does this kind of work.
Are there any tips for starting a woodworking enterprise?
It can be difficult to start a woodworking shop. If you are passionate about your hobby, it will not be difficult to put in the work. You will probably love the challenge of starting your own business.
Remember that you may encounter unexpected problems when starting a new venture. You might run out unexpectedly of funds. Or you might find that your customers aren’t willing or able to pay as much you had hoped. Preparedness is key to survival in such situations.
One tip is to have a separate banking account for your company. This way, you'll always know exactly how much money you have coming in.
Is it necessary to be a genius in woodworking to succeed?
No. Woodworking is not rocket science. Anyone can learn to use basic powertools and techniques to create beautiful work of art.
Statistics
- Most woodworkers agree that lumber moisture needs to be under 10% for building furniture. (woodandshop.com)
- Woodworkers on the lower end of that spectrum, the bottom 10% to be exact, make roughly $24,000 a year, while the top 10% makes $108,000. (zippia.com)
- The best-paid 10 percent make $76,000, while the lowest-paid 10 percent make $34,000. (zippia.com)
- In 2014, there were just over 237,000 jobs for all woodworkers, with other wood product manufacturing employing 23 percent; wood kitchen cabinets and countertop manufacturing employing 21 percent. (theartcareerproject.com)
External Links
How To
Tips on how to drive a nail in wood
First, choose the right size and type of tool to drive a nail through wood. The most common types of hammers are claw hammers, sledgehammers, mallets, ball peen hammers, and hatchets. Each kind of hammer has its own advantages and disadvantages. A claw hammer is best for hitting nails or hard objects. However, it can be difficult to pinpoint exactly where the blow will land. A sledgehammer is great for hitting large areas at once, but it's too heavy to use effectively for smaller tasks.
After you've chosen the right tool, hold your hand flat to the handle so it rests comfortably in one of your palms. Hold the handle in your hand, but don’t force it too hard that you break. Your wrist should be relaxed while you hold the hammer straight upwards. Next, swing the hammer toward the ground and aim for the nail's center. You should feel the impact of the hammer striking the nail. If you're having trouble getting the hang of swinging a hammer, practice with a block of wood until you get the rhythm down.
Once you are ready to drive the nail, place the hammer close to your body. Position the nail, so it's perpendicular to the surface of the wood. Keep your eyes focused directly on the tip of the nail. Swing the hammer forward, then follow through with the motion of the hammerhead. Keep doing this until you are comfortable with the swing. Once you've mastered the technique, try adding power to your swings. Try holding the hammer above your shoulder and bring it down forcefully. You will be able to use more energy and put your best foot forward.
Once you've nailed the first hole, remove the hammer from the nail. To remove the remainder of the nails, you can use a screwdriver/pry bar. Keep the nail heads parallel to the board's surfaces in order to avoid splitting wood.